
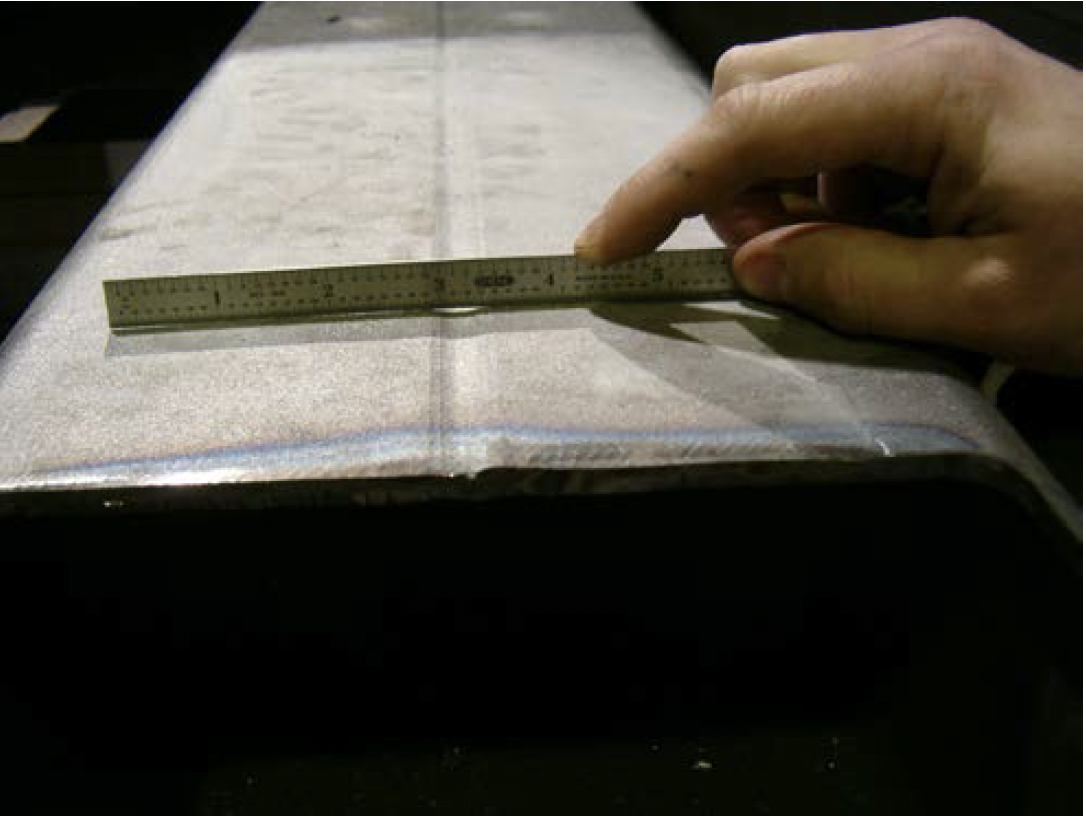
Radius of Corners – For square and rectangular structural tubing, the radius of each outside corner of the section shall not exceed three times the specified wall thickness.
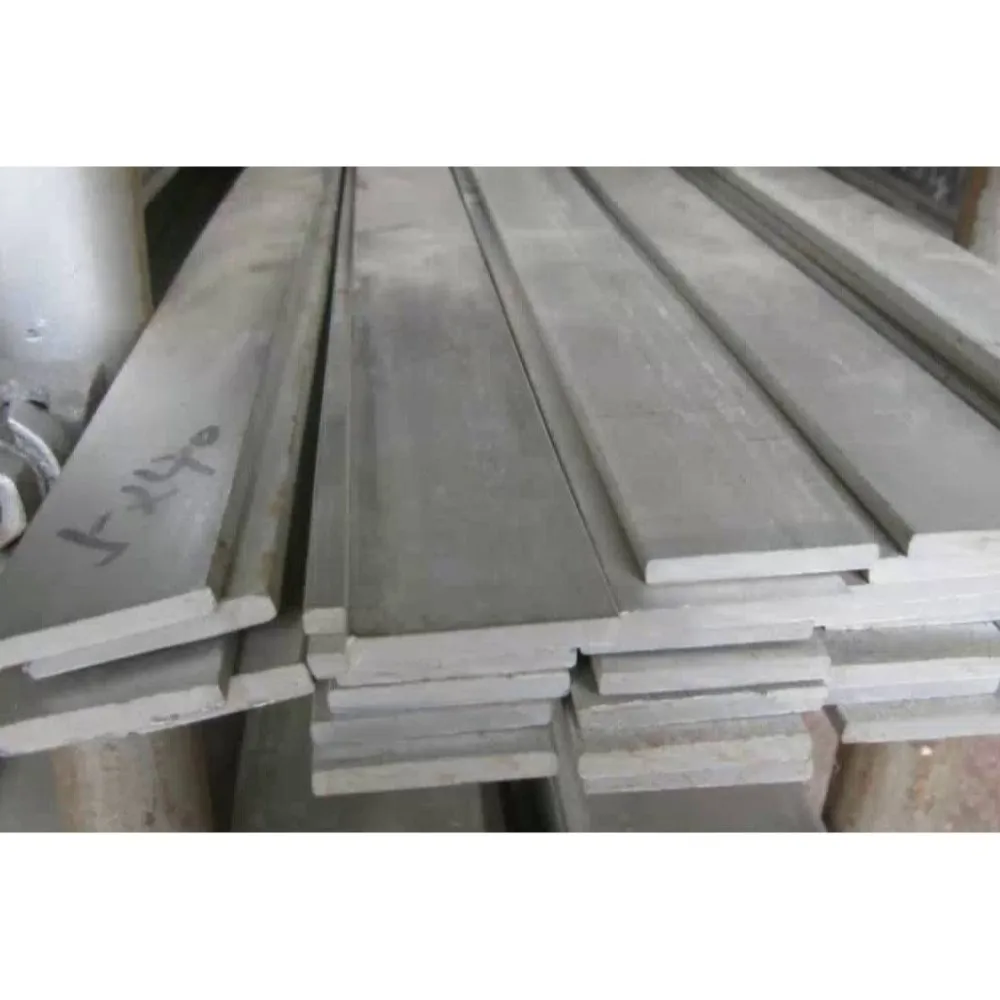
Squareness of sides – For square and rectangular structural tubing, adjacent side shall be square (90 degrees), with a permissible variation of +/-2 degrees maximum. times the number of feet of total length divided by 5. Straightness – The permissible variation for straightness of structural tubing shall be 1/8 in. HSS members can be circular, square, or rectangular sections, although. For rectangular tubing having a ratio of outside large to small flat dimension greater than 3.0, the permissible variations in small flat dimension shall be 2.0 times the permissible variations in large flat dimension. A hot-rolled HSS-box section cut open with a bandsaw, demonstrating residual stress. For rectangular tubing having a ratio of outside large to small flat dimension in the range of 1.5 to 3.0 inclusive, the permissible variations in small flat dimension shall be 1.5 times the permissible variations in large flat dimension.
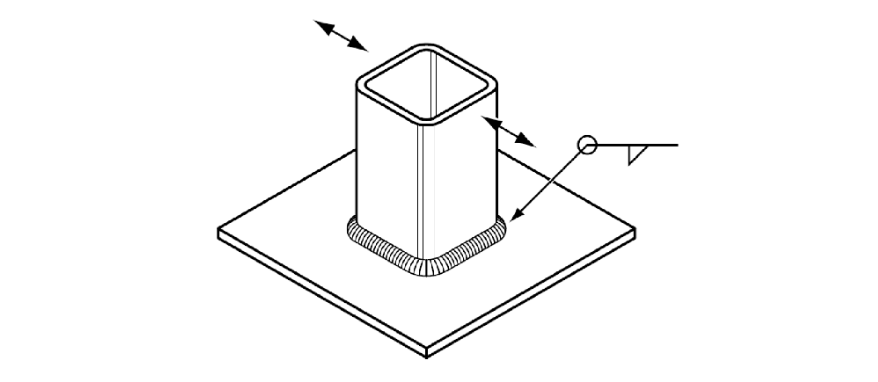
For rectangular tubing having a ratio of outside large to small dimension less than 1.5, and for square tubing, the permissible variations in small flat dimension shall be identical to the permissible variations in large flat dimensions.

*The permissible variations include allowances for convexity and concavity. Permissible Variations Over and Under Specified Outside Flat Dimensions,* in. Just practice and isstruction.Typical Permissible Variations in Outside Diameter Specified Outside Large Flat Dimension, in. If you have a process spec for welding thin carbon steel, you don't need another. Single U butt Both plates have a corner cut out in a ¼ moon shape about ¾ of the plate gauge deep to form a U partway through the joined sections, as the weld symbol shows. Remember, the purpose of the bevel in the weld prep is to ensure your welders can reach the inside of the weld on the first pass. With one square end and a 45° bevel on the other side only partly through the plate, the weld prep will look like its symbol, as a lowercase r without an arc. Here they will need to reduce heat, reduce feed rate of the wire, and work very hard not to make holes. On the outside, you will melt and round off the very skinny corner. on this corner, maybe a slightly slower speed, but a slightly higher wire feed rate or slightly higher heat input. If they use a MIG welding process, they will have to swing the nozzle across the joint to get the base metal in both tubes melted. On the inside corner, your welders will have a fillet joint that will tend to either burn through or not get good fusion into both tubes. Assume a weld heat or feed rate of 2 is used. (The 45 degree cut of both tubes is more important for your fitup!) Your first pass will completely fill the joint. 1/8 will be a bit easier to work with, but I'd worry much, much more about burning through and having to frequently "fill in" the hole rather than worry about the prep.Ī conventional 1/8 steel prep on the sides will have a 1/16 flat, then a 1/16 "bevel" - very difficult to machine accurately. Just fuse the two touching steel, working very hard not to burn through the wall. If you have 14 gage steel walls like I use for railing and frames, you can't really make any prep at all. Not real sure how you write a complete weld procedure for this joint: The sides are really just two simple thin piece of carbon steel, the inside is a tight 90 degree fillet, the outside corner is two flat pieces touching each other with a very, very thin sliver of steel at the extreme corner.ġx1x1/8 thick sq tubing is very thick, but you really don't have much metal there for any kind of "weld prep."
